GN 4.10 Maintaining sustainable energy and water assets
Guidance Note purpose
The purpose of this Guidance Note is to provide asset managers, property managers and facilities managers with information relating to the maintenance of low carbon energy systems and water efficiency infrastructure.
Context
Investment in low carbon energy systems and water efficient infrastructure continues to grow as businesses look for opportunities to reduce the energy and water intensity of their buildings and to achieve net zero carbon commitments and wider sustainability targets.
Factors to consider in the management of such sustainable energy and water infrastructure include:
- Maintenance.
- Regulatory compliance.
- Health and safety.
- Billing options.
For the purposes of this guidance note:
-
Low carbon energy systems cover:
- Photovoltaics.
- Heat networks.
- Heat pumps.
- Water efficiency infrastructure covers:
- Rainwater harvesting.
- Low flow appliances.
- Sustainable drainage systems.
Importance
Appropriate maintenance of low carbon energy systems and water efficiency infrastructure is often required as part of regulatory compliance. It is also important to maintain effective and safe operation of assets and to ensure that the projected energy, carbon and water savings are delivered.
Responsibilities & Interests
The table below summarises the key activities associated with electric vehicle charging provision, and highlights where asset managers, property managers and facilities managers are likely to have a responsibility or specific interest.
- AM - Asset Manager
- PM - Property Manager
- FM - Facilities Manager
1: Maintenance
Stakeholder:
2: Regulatory Compliance
Stakeholder:
3: Health & Safety
Stakeholder:
4: Billing Options
Stakeholder:
How to
Intro
Asset managers have an interest in the management of low carbon energy systems and water efficiency infrastructure due to their position as part of a property’s asset base and contribution to a property’s overall performance and commercial value. Property managers co-ordinate an agreed programme of management activities associated with these assets, with input from facilities manager.
Low carbon energy infrastructure - Photovoltaic (PV)
Description:
Photovoltaic (PV) devices convert sunlight into electricity via an electronic process that occurs naturally in specific materials called semiconductors. Single PV devices, known as cells, are connected together to form a panel or module.
Modules can be used on their own where the electricity demand is low or grouped to form an array where electricity demand is greater. A panel or array is located in a position and orientation which maximises the exposure to sunlight such as building roofs, above car park canopies or open spaces such as fields.
The electricity can either be consumed directly on site or fed back to the grid and consumed off site.
Benefits:
- Provide a building with a clean source of energy and play a role in how a building achieves net zero carbon
- Reduce a building’s demand for electricity from the grid
- The flexible size of the panels means that PV is suitable for all building types
- Maintenance requirements and costs are low
- Surplus electricity can be sold back to the grid and provide an additional income stream
Maintenance
Alongside general maintenance activities for all assets, maintenance considerations specific to PV include:
- Clean panels two to four times per year with water to make sure dirt and debris aren’t impacting the performance of panels. Avoid using abrasive materials to prevent damage.
- Check PV performance on a regular basis through meter reads or sensors to monitor the efficiency of panels.
- Contract a suitably qualified person, on an annual basis, to inspect for:
- Module fracture and moisture penetration.
- Damage to the direct current cables.
- Status of the surge protection devices.
- Inverter functionality.
- Low-voltage system connection.
It is also important to plan for modular replacement and appropriate disposal methods. Modules should not be disposed of with normal waste because burning or landfilling may release toxic compounds. Modules should be returned to the manufacturer or a safe disposal agent if damaged.
Regulatory compliance
There are no regulations which PV systems must comply with during operation. However, if you are installing PV then you may be required to comply with building regulations and obtain planning permission.
Health and safety
The primary health and safety concerns associated with PV relate to fire and electric shock.
Fire: There is no evidence that PV systems pose additional fire risks than other electrical equipment. However, appropriate steps should be taken to mitigate any risk of fire by a suitably qualified person regularly inspecting the system.
Common fire related faults include:
- Installation of AC (alternating current) isolator switches in DC (direct current), which causes heat to build up.
- Faulty inverters or lack of isolator switches.
Electrical shock: As PV systems use DC supply, in the event of a failure of the AC supply to the building, the PV system will still be live and may need to be manually isolated.
Billing options
There are a number of contractual models for the delivery and operation of PV:
- Building owner purchases PV up front or through finance agreement:
- Equipment purchased by building owner who owns the infrastructure.
- A fee is charged by an operator who manages and maintains the system.
- The building owner receives the full income from selling the electricity to occupiers or back to the grid (see Small Export Guarantee below).
- Space is leased to a 3rd party:
- Building owner has no upfront costs or operational costs to maintain the system. They do not own the system.
- Building owner can receive income through a rent for leasing space, this can be structured as a percentage of the profits from the operator selling the electricity or receiving free electricity for example.
- Through the Small Export Guarantee (SEG) small-scale electricity generators with capacity of up to 5MW can apply for a license and get paid for any surplus electricity that is generated which can be exported to the grid.
- Power Purchase Agreements is a long-term contract which can be set up whereby a consumer of electricity, such as an occupier, can be supplied with electricity directly from the installation on site at a pre-agreed price per unit of electricity.
Low carbon energy infrastructure - Heat Networks
Description:
A heat network is a central system which provides heating, cooling and hot water to occupiers who are re-charged for the service.
Heat networks can involve a single building with a minimum of two occupiers, a communal heat network, or multiple buildings which make up a district heating network.
A heat network can be supplied from various energy sources such as combined heat and power, energy from waste, fuel cells and heat pumps which all require specific maintenance regimes.
Benefits:
- Provides a low carbon option for heating a building.
- Heat that is being created through industrial or commercial processes that would otherwise be wasted is utilised.
- As there is no heat generation equipment in the building this results in less space required for plant, less requirement for maintenance and avoided costs for safety checks and inspections for boilers or CHP, for example.
- Improve local air quality by avoiding combustion of fossil fuels in urban locations.
- The price of heat is competitive if not less than gas and usually remains stable over the longer term.
Maintenance
If a property is heated via a district heating network with a 3rd party operator, there is little to no maintenance required above normal system and infrastructure checks. However, as heat networks often use water to transport heat, measures should be taken to prevent the risk of leaks within the property.
Specific consideration should be given to the maintenance of pipework and to pumps and values within heat networks
- Pipework
- Undertake regular inspections to ensure insulation is not damaged, leading to heat losses in the system and also to ensure there are no water leaks.
- Establish a water treatment regime to ensure good water quality to prevent damage to pipe work and other components through deposits of scale.
- Pumps and valves
Ensure all pumps and valves are checked and cleared regularly to ensure efficiency and to prevent interruptions to the service.
Regulatory compliance
Heat network operators in the UK must comply with the Heat Networks (Metering and Billing) Regulations (2014 and 2020).
The regulations require the heat network operator to:
- Notify the Office for Product Safety and Standards (OPSS) on or before the day the network becomes operational. The operator must submit a renotification within every four-year period from then on and inform the OPSS if the network is shut down.
- Fit heat meters, where appropriate, and maintain these to ensure continuous operation in measuring each occupier’s consumption.
- Bill occupiers fairly, transparently and based on actual consumption where cost effective to do so.
The template for submitting notifications, along with information to identify whether a property falls within the regulations and is required to install heat meters, is available here: government guidance on heat networks.
Health and safety
The primary health and safety concern associated with heat networks relates to legionella. Heat network operators that use water to transport heat should consider measures to avoid the growth of legionella.
Billing options
There are a number of contractual models for the delivery and operation of heat networks. The Greater London Authority describe four options alongside the associated contract requirements:
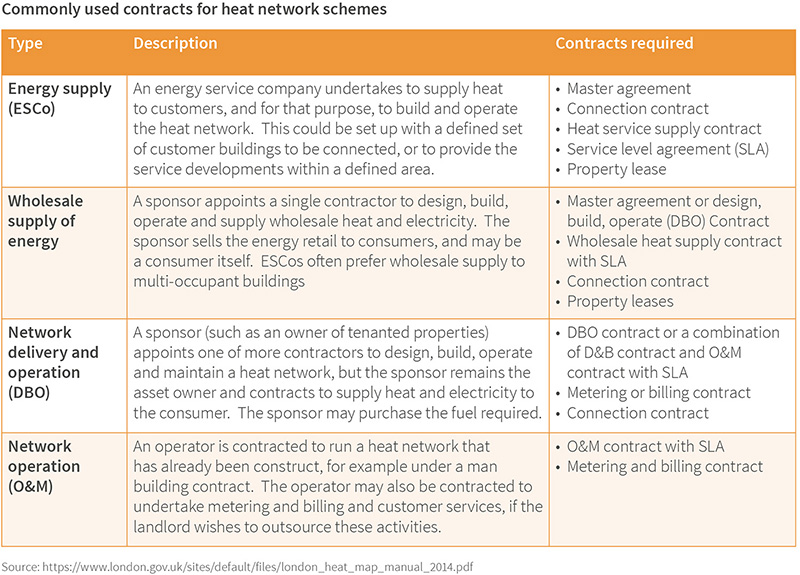
Low carbon energy infrastructure - Heat Pumps
Description:
A heat pump is a device used to heat and, in some cases, cool a building using air, ground or water heat. It does this by transferring thermal energy from a cooler space to a warmer space (or the reverse if cooling is required). A heat pump is typically made up of a condenser, evaporator, compressor and expansion valve and they are an efficient alternative to conventional fossil fuel heating systems.
In an open loop system fluid flows through the system and is not recirculated. For example, groundwater can be pumped through the system and discharged back into the ground or at the surface.
In a closed loop system a mixture of water and antifreeze circulates within a system and is constantly recirculated.
Benefits:
- Reduces carbon emissions for heating and cooling buildings when compared with conventional solutions.
- One system provides both heating and cooling.
- While the capital investment in heat pumps is usually higher than conventional heat systems, as heat pumps are more efficient the running cost are lower once in operation.
- Heat pumps are safer and require less maintenance than combustion systems.
- Government schemes may be available to support with the initial investment in a heat pump.
Maintenance
Alongside general maintenance activities for all assets, maintenance considerations specific to heat pumps include:
- On a monthly basis check the air filters, cleaning or replacing as appropriate, check for ice, corrosion or leaks.
- Debris may collect in open loop systems and lead to potentially costly repairs. Every two or three months the heat exchangers, pipework and pumps should be checked for corrosion, bacterial growth or mineral deposit and cleaned as appropriate to prevent build up.
- On an annual basis a specialist contractor should service the heat pump whilst also undertaking electrical safety and control system checks.
- For closed loop systems the specialist contractor should also check for biological contamination and undertake a refrigerant gas leak test. They should inspect the level of antifreeze, biological growth inhibitor and corrosion inhibitor.
- A log should be kept of any maintenance, improvements, changes or issues such as refrigerant gas leakages.
- It is mandatory for systems equivalent to 500 tonnes or more of carbon dioxide to be fitted with an automatic leak detection system. Ideally, this should be considered for all systems.
Regulatory compliance
- If the heat pump system uses refrigerant gases, then compliance with the European Union F-Gas regulations or UK equivalent regulations is required. This includes the following:
- Service and maintenance bans – there are limits on the use of gases with high Global Warming Potential (such as R404A and R507A) in existing equipment from 2020.
- Leakage controls – there is an increased requirement for leak checks, leak detection systems and associated record-keeping.
- Responsible supply – a requirement that gases are sold, managed and used by trained individuals. The individual undertaking maintenance must be suitably qualified and have the appropriate level of certificate to carry out maintenance activities. Full details can be found on the government’s website.
- Leak checking under the F-Gas Regulations is a requirement and there are different frequencies of checks depending on the size of the system – see table (end). UK Government guidance states that you must repair a leak as soon as possible and test the system within a month. If you do not have a leak checking system in place or do not fix leaks there is a risk of receiving a penalty from the Environment Agency.
- Additionally, if you are installing new heat pumps then you will be required to comply with building regulations.
Health and safety
There are a number of health and safety risks:
- Electrical safety: Any electrical installation, maintenance or repair of the heat pump system should be undertaken by a suitably qualified electrician.
- Refrigerant leakage: Refrigerants present a number of risks such as explosion, toxicity, air displacement and cold burns. It is important that a suitably qualified specialist maintains the system and that a leak detection system is in place.
- Water: Heat pump systems that use water should be maintained in line with other water systems to prevent bacterial growth such as Legionella.
Billing options
The billing system can be exactly the same as a building providing heating or cooling via conventional systems.
There is a government Renewable Heat Incentive (RHI) which is a scheme that would provide financial support for the installation of heat pumps. There are separate schemes for domestic and non-domestic buildings.
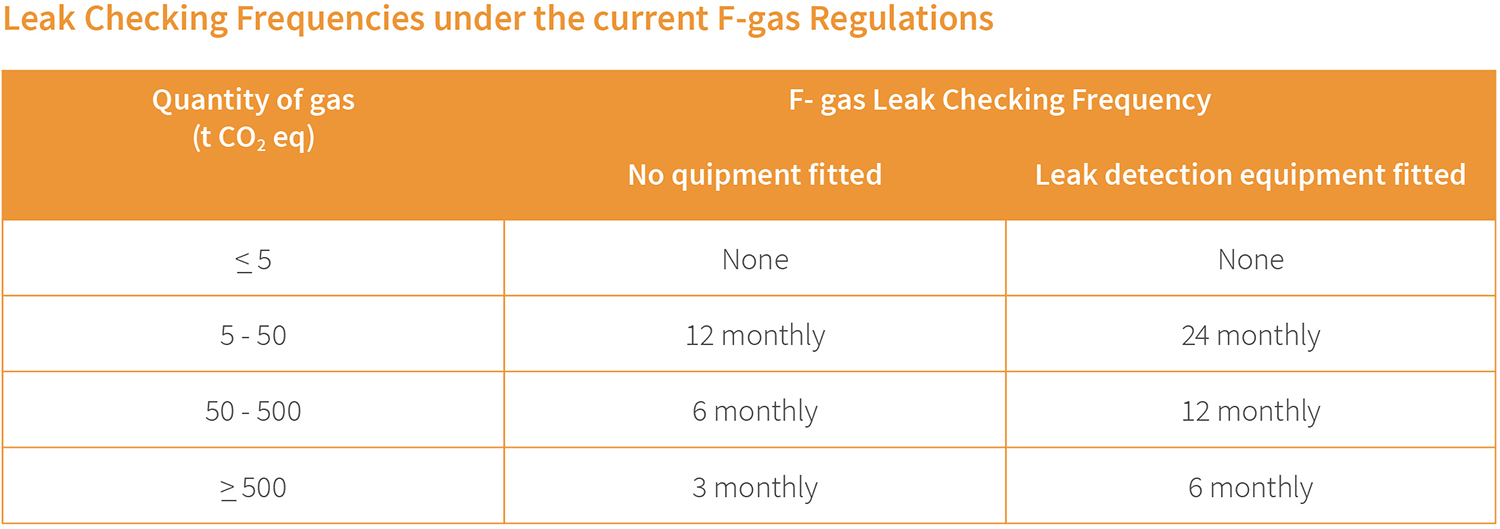
Water efficiency infrastructure - Rainwater harvesting
Description:
A rainwater harvesting system collects, stores and allows the reuse of rainwater running off surfaces upon which it has fallen. The water is typically used for non-potable uses such as toilet flushing or landscape watering.
Benefits:
- Reducing costs associated with purchasing supplies from a water company.
- Reducing the energy consumption and carbon emissions associated with a building’s water use.
- Rainwater harvesting reduces flash-flood risk associated with heavy rainfall.
- Reuse of water reduces the amount of sewerage discharge and the associated financial costs.
Maintenance
Specific consideration should be given to the following maintenance aspects in relation to rainwater harvesting infrastructure:
- Every two-three months, clear debris from pre-tank filters and clean gutters to maintain efficiency and reduce having to top the tank up from mains water.
- Every year, service the system, including visually and electrically checking pumps and electrically, check the condition of flexible hoses, seals and fixings of lids, cables and connectors.
- Regularly checking the solenoid valve needs with a mains water top up to prevent leakages or the tank not filling up properly.
Regulatory compliance
There are no regulations that must be complied with for rainwater harvesting in operation. However, in most cases, before work starts on installing rainwater harvesting, consent must be obtained from the water supplier by giving notification of the details of the proposed infrastructure as part of compliance with The Water Supply (Water Fittings) Regulations (1999).
Health and safety
There are low health and safety risks when using rainwater for non-potable uses such as toilet flushes.
Billing options
Billing considerations for rainwater harvesting should consider:
- Inclusion of maintenance costs as part of the wider contract.
- Recognition of the reduced cost of potable water as part of a property’s water bill.
Water efficiency infrastructure - Low flow appliances
Description:
Low flow appliances include systems such as low flow toilets and taps, tap and shower aerators and flow controllers.
Benefits:
- Reduce the amount of potable water a building consumes and as a result also reduce expenditure on water bills.
- The initial cost of installing or retrofitting low flow appliances are slightly higher, if not comparable with regular appliances but have a lower whole life cost due to their efficiency.
Maintenance
Specific consideration should be given to the following maintenance aspects in relation to rainwater harvesting infrastructure:
- Every two-three months, clear debris from pre-tank filters and clean gutters to maintain efficiency and reduce having to top the tank up from mains water.
- Every year, service the system, including visually and electrically checking pumps and electrically, check the condition of flexible hoses, seals and fixings of lids, cables and connectors.
- Regularly checking the solenoid valve needs with a mains water top up to prevent leakages or the tank not filling up properly.
The following elements should be considered as part of a maintenance regime for low flow appliances:
- Make periodic adjustments to flow-control devices, check automatic valves are functioning properly.
- Replace automatic control batteries regularly.
- Avoid using harsh chemicals and pouring water down waterless urinals as this will damage the trap/cartridge system which acts as the urinal’s flush.
- When the cartridge is removed for replacement (usually every fourth year), water can be flushed down the system before installing a new cartridge.
- Check aerators regularly, removing and cleaning any debris or dirt and look to replace annually to avoid limescale build up
Regulatory compliance
There are no specific regulations that must be complied with for low flow appliances in operation.
Health and safety
Typically, there are no greater health and safety risks to low flow appliances than regular appliances. Regular cleaning regimes will eliminate and reduce the risk of bacterial growth and viruses.
Billing options
Billing considerations for low flow appliances should consider:
- Inclusion of maintenance costs as part of the wider contract.
- Recognition of the reduced cost of potable water as part of a property’s water bill.
Water efficiency infrastructure - Sustainable Urban Drainage (SuDS)
Description:
SuDS are a natural approach to managing draining in and around a building or development. They are a collection of water systems that mimic the natural water cycle and reduce the risk of flooding by slowing and holding surface water drainage from running off a site too quickly.
Benefits:
- SuDS are a natural method for managing flood risk and reduce the risk of flooding in the vicinity of the building.
- By imitating the natural water cycle, SuDS reduce the transportation of pollutants to the watercourses as they are removed whilst the water travels through the ground.
- Groundwater sources are under pressure in the UK and SuDS can be used to recharge these vital sources of water.
- SuDS are often combined with green infrastructure and therefore create an opportunity to provide new habitats for wildlife and support local biodiversity.
Maintenance
Specific consideration should be given to the following maintenance aspects in relation to SUDs:
- Monthly:
- Remove debris, litter and cut surrounding grass.
- Inspect inlets, outlets and flow control systems.
- Sweep permeable paving.
- Inspect for damage and undertake remedial work if required.
- Annually:
- Remove silt from that has built up in the system.
- After leaves have fallen, sweep permeable paving and remove debris.
- Avoid using weedkillers and pesticides to prevent chemical pollution.
Regulatory compliance
There are no regulations that must be complied with for SUDS in operation. However, there are non-statutory technical standards, which have been developed by DEFRA for England and Wales.
In addition, some local authorities have their own policy and guidance which the design and installation must comply with.
Health and safety
The primary health and safety concern associated with SUDs relate to flood risk, deep water and slips/trips/falls. Consideration should be given to:
- Undertaking a site evaluation to identify flood risks which pose a threat to safety and put plans in place to mitigate. These will typically be blocked pipes, failure of pumps, unexpected impediments across planned flood or exceedance routes.
- Mitigation measures relating to deep water, such as, for example, fencing, signs and life-saving equipment.
Mitigation measure relating to slips or falls as a result of wet conditions, such as, for example, regular cleaning to prevent algae build up, closure of paths in wet or icy conditions and signage.
Billing options
Unless there is a separate agreement, the asset manager is usually the default party responsible for maintaining the SuDS components. However, through contractual agreement and payment, this responsibility can be given to a specialist organisation who ‘adopt’ the system.
Related Guidance Notes
The following Guidance Notes contain related information:
- GN2.1: An asset register
- GN2.4: Maintenance, monitoring and the property management cycle
- GN4.8: Template action plan
- GN4.9: Energy efficiency opportunities
- GN4.11: Procuring renewable energy
- GN5.4: Water efficiency opportunities
- GN7.2: Electric vehicle charging facilities
- GN11.3: Service charge considerations
Additional Resources
PV:
UK Government: Government studies on fires involving PV
UKGBC: Renewable Energy Procurement & Carbon Offsetting Guidance for Net Zero Carbon Buildings
OFGE: About the Smart Export Guarentee
Heat Networks:
UK Government: Heat Network Guidance
Heat Pumps:
UK Government: FLourinated gas (F Gas): guidance for users, producers and traders
Rain water harvesting:
BS 8515:2009 'Rainwater Harvesting Systems, Code of Practice'
SUDs
UK Government: Non-statutory Standards for SUDS
Welsh Government: Statutory standards for sustainable drainage systems